РАЗДЕЛ III
ОРГАНИЗАЦИЯ ДЕЯТЕЛЬНОСТИ ПРЕДПРИЯТИЯ
ТЕМА 19
ОРГАНИЗАЦИЯ ПРОИЗВОДСТВА
19.8. Поточное производство
Поточная организация производства -
это такая форма организации производства, при которой операции выполняются в
определенной, заранее
установленной
последовательности; имеют равновеликие задачи по выпуску предметов труда за тот
же период и выполняются одновременно. На предприятии применяется поток с
свободным темпом - агрегатно - групповой. Эта система организации потоков
характеризуется повышенной изменяемостью ассортимента продукции, применением
агрегированного оборудования. Смена моделей в агрегатно-групповом потоке не
вызывает перестройки рабочих мест, а ограничивается сменой приспособлений,
перемещением одного или нескольких исполнителей с одного рабочего места на другое.
Поточное производство - это наиболее
эффективная форма организации производства по массовому выпуску продукции,
обеспечивает высокий рост производительности труда, непрерывность производственного
процесса и высокий уровень качества.
Особенность организации потокового
производства на современном этапе является управление большими коллективами людей и
динамика развития отраслей промышленного производства, т.е. быстрая зміщуваність
видов продукции.
Поточное производство заключается в
объединении машин, что делают аналогичный вид или тип продукции. Различаются
два варианта: группа машин и производственные линии.
Если говорить о группе машин, то
речь идет о оборудование, размещенное в зависимости от последовательности операций.
Когда речь идет о производственную линию, то
оборудование размещают по прямой линии; цеха - на параллельные линии,
специализируются на определенном товаре (или типах товаров).
При организации поточного
производства необходимо учитывать длительность заказа, объем выпуска,
определить категорию качества и технический уровень производственных звеньев. При поточном
производстве чаще используют поточные линии.
Поточная линия - это группа рабочих
мест, расположенных в строгой последовательности операций технологического цикла, по
которыми закреплены определенные операции. Несколько поточных линий составляют цех.
Основные характеристики поточной
линии:
1. Закрепление за каждым рабочим
место только одной операции по изготовлению деталей или сбора продукции.
2. Расположение рабочих мест по
ходу линии.
3. После окончания операции на
следующее рабочее место детали передают по одной.
4. Синхронизация продолжение
каждой операции технологического процесса на поточной линии. То есть операции
должны быть кратны такту линии.
5. Механизация передачи деталей и
изделий с одного рабочего места на другое.
6. Замкнутый характер производства,
который включает все работы по изготовлению деталей и изделий.
Поточные линии могут отличаться
друг от друга по следующим характеристикам:
- номенклатура изделий,
изготавливаются;
- уровень безупинності процесса;
- уровень механизации и
автоматизации;
- условия наладки оборудования и др.
При организации поточных линий
рассчитываются:
- такт;
- число рабочих мест и рабочих
на поточной линии;
- синхронизация операций;
- скорость движения и длина
рабочей ленты конвейера;
- производственные нормативы.
Основными направлениями улучшения
работы поточных линий могут быть:
- снижение простоев оборудования;
- своевременное подачи сырья и
материалов;
- рационализация рабочих мест
потока;
- улучшение условий труда на
рабочих местах;
- синхронизация работы потока;
- введение багатоверстатного
обслуживание и совмещение профессий.
При организации производственных участков в
условиях потока большое значение имеет правильный выбор транспортных средств -
наиболее эффективными транспортными средствами являются конвейеры.
Существуют три вида конвейеров:
непрерывный, пульсирующий и распределительный. Пульсирующий конвейер характеризуется
тем, что изделие снимается с линии и обрабатывается на рабочем месте, затем изделие
возвращается на линию, осуществляет его транспортировку на другое рабочее место.
Условием работы этой линии является равенство такта сумме времени обработки детали и времени
транспортировку.
Для организации потокового
производства во времени применяется три вида движения предметов труда: последовательный,
параллельный и смешанный.
Последовательный вид движения предметов труда
имеет максимальное время сборки и, как следствие, высокую себестоимость.
Параллельный вид движений предметов
труда имеет минимальное время сборки всех видов движения предметов труда, но требует
обязательной кратности времени обработки изделия на всех операциях, а лучше -
равенства. Себестоимость минимальная.
Смешанный вид движения предметов труда
имеет среднее время сборки изделия по сравнению с параллельным и последовательным видами
и среднее значение себестоимости. При этом виде детали могут передаваться как
поштучно, так и сериями или партиями, что исключает недостатки по продолжительности
составление и перезагрузке или недозавантаженню рабочих мест, что характерно
для первых двух видов. Более подробно этот вопрос рассмотрен. 8 этого
раздела.
Поточный метод организации можно
применять с соблюдением следующих условий:
а) объем выпуска продукции достаточно
большой и не изменяется в течение длительного периода времени;
б) конструкция изделия
технологична, отдельные узлы и детали подвергаются транспортировке, изделие можно
делить на конструктивно-сборочные единицы, что особенно важно для организации
потока с составления;
в) затраты времени по операциям могут
быть установлено с достаточной точностью, синхронизированы и сведены к единой
величине; обеспечивается непрерывная подача к рабочим местам материалов,
деталей, сборочных узлов; возможна полная загрузка оборудования.
Организация поточного производства
связана с проведением ряда расчетов и подготовительных работ, которые связаны с
аппаратурно - механическим оснащением производства и согласования всех его
элементов.
Исходным моментом при проектировании
объема выпуска продукции является такт потока.
Такт - это промежуток времени между запуском
(или выпуском) двух смежных изделий на линии. Такт может быть и средним
рабочим.
Средний такт потока - это календарный
период времени между двумя последовательными выпусками или запусками продукции на
текущей линии.
Средний такт определяется по
формуле
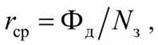
где
Фд - действительный фонд времени работы линии за определенный период (месяц,
сутки, смену) с учетом потерь на ремонт оборудования и регламентированных
перерывов, мин.;
Nс - программа запуска за тот же период
времени, пит.

где
N - программа выпуска, пит.;
(100-δ)
- процент отсева на контрольные испытания и брак.
Продолжительность расчетного периода
[действительный фонд времени работы линии за определенный период (месяц, сутки, смену) с
учетом потерь на ремонт оборудования и регламентированных перерывов]
рассчитывается по формуле:

где
К - количество рабочих дней в месяц,
дн.;
С - количество смен в сутки, шт.;
Т - продолжительность смены, ч.;
а - доля времени на регламентированные
простои, перерывы, подготовку к работе и уборка рабочего места и т.п.
Рабочий такт - это часть продолжительности
операции на одном рабочем месте. Рабочий такт определяется по формуле:
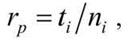
где
ti - продолжительность каждой операции;
ni - число рабочих мест на данной
операции.
Такт поточной линии - это интервал
времени, за который сходят с линии изделия, передвигаются друг за другом.
Определяется из выражения
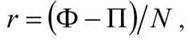
где
Ф - суточный фонд времени;
П - технически неизбежные затраты времени, мин.
(15-20 мин. за смену);
N - объем производства продукции за
тот же период в натуральном измерении.
Величина, обратная такту,
называется темпом работы линии. При организации поточного производства
необходимо обеспечить такой темп, чтобы выполнить план по выпуску продукции.
Расчетная формула такая:
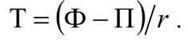
Если предметы труда передаются не
поштучно, а транспортными партиями (п), то они сходят с линии за интервал
времени, что называется ритмом линии:
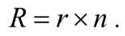
Следующим этапом в организации
поточного производства является определение потребности в оборудовании. Расчет
количества оборудования осуществляется, исходя из количества рабочих мест за
операциям процесса:
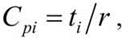
где
ti - норма времени на операцию с
учетом установки, транспортирования и снятия детали, мин.
Принятое количество рабочих мест (Сри)
определяется округлением расчетного количества до ближайшего целого числа.
При этом учитывается, что на стадии проектирования допускается перегрузка в
пределах 10-12 % на каждое рабочее место.
Количество рабочих мест на поточной
линии определяется по формуле
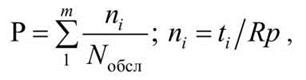
где
m - количество операций на потоке.
Длина ленты конвейера
определяется так:
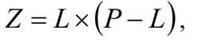
где L - расстояние между рабочими местами.
Скорость конвейера
определяем из выражения
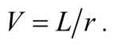
Для обеспечения полного
загрузки оборудования и непрерывности протекания производственного процесса в
поточном производстве осуществляется синхронизация (выравнивание) операций в
времени.
После того как достигнуто
синхронизацию операций на поточной линии, составляется план-график ее работы,
что облегчает контроль за использованием оборудования и рабочих.
Одним из основных условий непрерывной
и ритмичной работы поточных линий является организация межоперационного транспорта. В
поточном производстве транспортные средства используются не только для
перемещения изделий, но и для регулирования такта работы и распределения предметов
труда между параллельными рабочими местами на линии.
Выбор транспортного средства зависит
от габаритов, массы обрабатываемых деталей, типа и количества оборудования, такта,
степени синхронизации операций.
Проектирование потока завершается
разработкой рационального планирования линии. В процессе планирования необходимо
придерживаться таких требований: предусмотреть удобные подходы к рабочим местам для
ремонта и обслуживания линии, обеспечить непрерывное транспортирование деталей
в разных рабочих мест на линии; выделить площадки для накопления задела
и подхода к нему; предусмотреть на линии рабочие места для выполнения контрольных
операций.
Метод групповой организации
производства применяется в случае ограниченной номенклатуры конструктивно и
технологически однородных изделий, изготовляемых повторяющимися партиями. Суть
метода заключается в сосредоточении на участке различных видов технологического
оборудования для обработки группы деталей по унифицированным технологическим
процессом.
Характерными признаками организации
производства являются: подетальная специализация производственных подразделений; запуск деталей
в производство партиями по специально разработанным графикам; параллельно-последовательное
прохождение партий деталей по операциям; выполнение на участках (в цехах)
технологически завершенного комплекса работ.
Метод организации синхронизированного
производства интегрирует ряд традиционных функций организации производственных процессов:
оперативного планирования, контроля складских запасов, управление качеством
продукции. Суть метода сводится к отказу от производства продукции крупными
партиями и созданию непрерывно-поточного багатопредметного производства, в
котором на всех стадиях производственного цикла требуемый узел или деталь
поставляется к месту последующей операции точно в необходимое время.
Поставленная цель реализуется за
посредством создания групповых, багатопредметних поточных линий и использования
принципа вытягивания в управлении ходом производства. Основными правилами
организации производственного процесса в этом случае являются:
- изготовление продукции мелкими
партиями;
- формирование серий деталей и
применение групповой технологии с целью сокращения времени отладки
оборудования;
- преобразование складов материалов
и полуфабрикатов на буфер-склады;
- переход от цеховой структуры
производства к предметно-специализированных подразделений;
- передача функций управления
непосредственно исполнителям.
Метод синхронизированного производства
предполагает внедрение системы комплексного управления качеством, которая основывается
на соблюдении следующих принципов: контроль производственного процесса; наглядность
результатов измерения показателей качества; соблюдение требований к качеству;
самостоятельное исправление брака; проверка 100 % изделий; постоянное повышение
качества.
Производство массовыми партиями
составляло и составляет на многочисленных предприятиях основной тип производства, оно
является апогеем тейлористської индустриальной культуры. В ситуации, когда основной
формой конкурентной борьбы является ценовая, приоритет отдается экономике с массовым
производством (большими партиями), а также процесса стандартизации продукции
(когда клиент ограничивается относительно небольшим выбором) и стандартизации операций,
последствия от которой выступают в виде разделения задач и возможностей прибегнуть к
квалифицированной рабочей силы, узко специализированной и незначительно связанной с
самим процессом производства. Производство массовыми сериями означает производство
максимально крупными партиями, где изменение орудий труда сведено к минимуму, для
того чтобы сократить до минимума затраты при выпуске большого количества продукции.
Много иностранных конкурентов
выступают за поточную систему производства с «выталкиванием» обрабатываемых
изделий, которая предусматривает более тесную координацию работу производственных участков. В
этом случае обрабатываемые изделия последовательно «вытягивают» с предыдущего участка в
мере необходимости. Такие производственные системы обычно достаточно просты по структуре.
Передача информации от участка к участку в основном осуществляется за
помощью бумажных карточек («канбан»), а не с помощью ЭВМ. Функционирования
таких систем в значительной степени определяется взаимодействием соседних производственных участков.
Использование иностранными фирмами
системы «поточного производства» является мощнейшим рычагом поддержки
американской экономики в лидирующей группе мировых экономически развитых стран.