РАЗДЕЛ III
ОРГАНИЗАЦИЯ ДЕЯТЕЛЬНОСТИ ПРЕДПРИЯТИЯ
ТЕМА 19
ОРГАНИЗАЦИЯ ПРОИЗВОДСТВА
19.5. Производственный цикл, его характеристика
и структура
Производственный цикл - один из
важнейших показателей, который является основой для расчета многих других
показателей производственно - хозяйственной деятельности предприятия. Например, на
основе производственного цикла устанавливаются сроки запуска изделий в производство,
рассчитываются мощности производственных подразделений, определяется объем
незавершенного строительства и некоторые другие показатели.
Производственный цикл - это календарный
период времени, в течение которого изделие или партия изделий, обрабатываемых
проходят все операции производственного процесса или определенной его части и
превращаются в завершенный продукт.
Интервал календарного времени от
начала первой производственной операции до окончания последней называется
длительностью производственного цикла во времени, которая измеряется в днях, часах, минутах,
в зависимости от вида изделия и стадии обработки.
Производственный цикл включает:
Время выполнения технологических операций
- основная составляющая производственного цикла, которая необходима для осуществления конкретных
рабочих операций преобразования предмета труда в готовую продукцию.
Подготовительно-заключительное время выделяется работнику для ознакомления с
сдачей и для сдачи готовой продукции. Продолжительность операционного цикла
состоит из времени выполнения технологической операции и подготовительно-заключительного
времени, то есть продолжительность операционного цикла - это время обработки одной партии
деталей на конкретной операции технологического цикла.
Продолжительность прохождения природных
процессов определяется особенностями технологии (это время твердения бетона,
охлаждение металла и т.п.), то есть природные процессы характеризуются только
затратами времени.
Продолжительность обслуживающих процессов
состоит из времени выполнения контрольных операций, складских и транспортных
(включая погрузку и разгрузку) операций. Совокупность всех составляющих
производственного процесса образует его рабочий период.
Часть производственного цикла - это
перерывы, которые состоят из межоперационных и міжзмінних перерывов.
Межоперационные перерывы образуют:
- перерывы между партиями -
возникают во время обработки партии деталей, ведь не все детали обрабатываются
одновременно. Сокращать эти перерывы можно за счет сокращения объема
транспортных партий деталей, однако это потребует увеличения затрат на
транспортировка деталей между рабочими местами;
- перерывы ожидания возникают
при нарушении хода выполнения технологического процесса, когда предыдущая технологическая
операция уже закончилась, а рабочее место на следующей операции еще не
освободилось от выполнения определенной работы;
- перерывы комплектования -
возникают на сборочных операциях, когда на место сборки поступают не все
наименование деталей.
Междусменные перерывы (обед, выходные
и праздничные дни, между изменениями) является неотъемлемой составной частью производственного
процесса.
Длительность производственного цикла (Тв)
определяется по формуле

где
Тоц - продолжительность операционного цикла;
Тпр - продолжительность
прохождение природных процессов;
Тобсл - продолжительность
обслуживающих процессов;
Тпер - время міжоперіційних
и міжзмінних перерывов.
Продолжительность производственного цикла охватывает
три стадии:
- время технологического оборудования;
- время технического обслуживания
производства;
- продолжительность перерыва.
Продолжительность производственного цикла
зависит от:
- продолжительности рабочего времени,
необходимого для производства продукции;
- размера партии;
- продолжительности перерывов в процессе
производства;
- длительности операций, прямо не
связанных с производственным процессом.
Время выполнения основных операций обработки
изделия составляет технологический цикл, что означает время, в течение которого
обрабатывается предмет труда. На длительность рабочего периода оказывает влияние ряд
факторов, главные из которых:
- качество
проектно-конструкторских работ;
- уровень стандартизации изделий;
- организационные факторы.
Время технологического обслуживания
включает в себя контроль качества обработки изделия, контроль режима работы машин
и оборудования, уборка рабочего места, время доставки деталей к рабочему
места.
Время перерывов - это время, в течение которого
не меняются никакие качественные характеристики изделия, но продукция еще не является готовой и процесс производства не закончен.
Различают регламентированные и нерегламентированные перерывы.
На предприятии выделяют следующие виды
перерывов:
- междусменные, которые зависят от
режима работы предприятия, количества смен, а также количества праздничных и
выходных дней;
- перерывы ожидания, связанные
с загрузкой оборудования;
- перерывы партионности, что
возникающие при обработке деталей партиями;
- перерывы, обусловленные
несовершенной организацией производственного процесса и непредвиденными обстоятельствами
(отключение электроэнергии, сбои в работе оборудования и т.д.).
Структура производственного цикла представлена
на рис. 19.3. Основной составляющей производственного цикла является продолжительность технологических
операций, которая составляет технологический цикл.
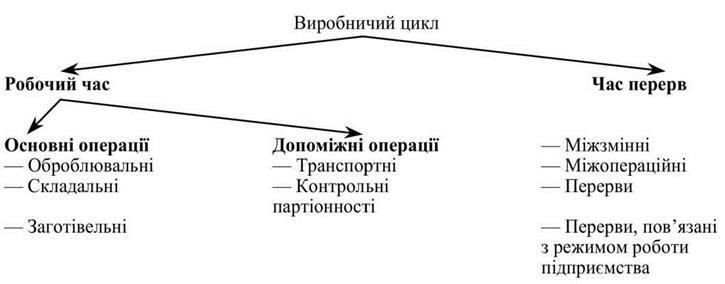
Рис. 19.3. Структура производственного
цикла
Технологический цикл обработки партии
предметов на одной операции равна
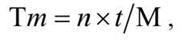
где Тm - технологический цикл в единицах
времени, минут;
n - количество предметов в партии;
t - продолжительность обработки одного
предмета;
М - количество рабочих мест, на которых
выполняется операция.
При расчете продолжительности
технологического цикла необходимо учитывать особенности передвижения предметов
труда по операциям. На предприятии используется один из следующих видов движения:
- последовательный;
- параллельный;
- параллельно-последовательный
(смешанный, совмещенный).
Как уже отмечалось, за превращение
предметов труда на конкретное изделие они проходят через множество основных,
вспомогательных и обслуживающих процессов, происходящих параллельно, параллельно-
последовательно или последовательно во времени в зависимости от сложившейся на предприятии
производственной структуры, типа производства, уровня специализации производственных
подразделений, форм организации производственных процессов и других факторов. Совокупность
этих процессов, обеспечивающих изготовление изделия, принято называть производственным
циклом, основными характеристиками которого являются его продолжительность и структура.
Продолжительность производственного цикла
изготовления продукции - это календарный период времени, в течение которого сырье,
основные материалы, полуфабрикаты и готовые комплектующие изделия превращаются
на готовую продукцию. Другими словами - это отрезок времени от момента начала
производственного процесса до момента выпуска готового изделия или партии деталей,
сборочных единиц. Продолжительность производственного цикла обычно отражается в
календарных днях или часах.
Знание продолжительности производственного цикла
изготовление всех видов продукции необходимо для:
- составление производственной программы
предприятия и его подразделений;
- определение сроков начала
производственного процесса по данным сроков его окончания;
- расчетов нормальной величины
незавершенного производства.
Структура и продолжительность производственного
цикла зависят от типа производства, уровня организации производственного процесса и
других факторов. Для изделий машиностроения характерна высокая доля
технологических операций в общей продолжительности производственного цикла. Сокращение
последней имеет большое экономическое значение. Как правило, длительность производственного
цикла определяется для одной детали, партии деталей, одной сборочной единицы
или партии единиц одного изделия. При этом стоит учитывать, что изделием
называют любой предмет или набор предметов, подлежащего изготовлению на
предприятии или в его подразделениях.
При расчете продолжительности производственного
цикла изготовления изделия учитывают только те затраты времени на транспортные и
контрольные операции, естественные процессы и перерывы, которые не перекрываются
операционным циклом.
Сокращение длительности производственного
цикла имеет важное экономическое значение. Чем меньше продолжительность производственного цикла,
тем больше продукции за единицу времени при прочих равных условиях можно выпустить на
данном предприятии, в цехе или на участке; тем выше использование основных
фондов предприятия; тем меньше потребность предприятия в оборотных средствах,
вложенных в незавершенное производство, тем выше фондоотдача и т. д.
В практике промышленных предприятий
производственный цикл сокращается одновременно по трем направлениям:
- уменьшается время трудовых
процессов;
- сокращается время природных
процессов;
- вполне ликвидируются или
сводятся к минимуму перерывы всех видов.
Практические мероприятия по сокращению
производственного цикла вытекают из принципов построения производственного процесса и
прежде всего из принципов пропорциональности, параллельности, непрерывности,
прямо-точности, ритмичности и др.
Пропорциональность - принцип, выполнение
которого обеспечивает равную пропускную способность разных рабочих мест одного процесса,
пропорциональное обеспечение рабочих мест информацией, материальными ресурсами,
кадрами и т. д. Пропорциональность определяется по формуле
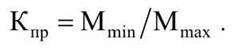
Сокращение времени трудовых процессов в части
операционных циклов достигается путем усовершенствования технологических процессов, а
также повышения технологичности конструкции изделия.
Под усовершенствованием технологических
процессов понимают их комплексную механизацию и автоматизацию, внедрение
скоростных режимов (например, скоростного и силового резания, скоростного
нагрев под ковку и штамповку), штамповки вместо свободной ковки,
литье в кокиль и литье под давлением вместо литья в песчаные формы, а также
концентрацию операций. Последняя может заключаться в багатоінструментальному и
багатопредметному разделке или в представлении в одном рабочем цикле нескольких
различных технологических операций (например, за объединение скоростного
индукционного нагрева со штамповкой заготовки в одном рабочем цикле ковочной
машины).
Повышение технологичности
конструкций изделий заключается в максимальном приближении последних к требованиям
технологического процесса. В частности, рациональное расчленение конструкции изделия
на узлы и мелкие сборочные единицы является важным условием для параллельного их
составления, а следовательно, и для сокращения длительности производственного цикла сборочных
работ.
Продолжительность транспортных операций
может быть значительно уменьшен в результате перепланировки оборудования на основе
принципа прямоточности, механизации и автоматизации подъема и перемещения
продукции с помощью различных подъемно-транспортных средств.
Сокращение времени контрольных операций
достигается путем их механизации и автоматизации, внедрения передовых
методов контроля, совмещения времени выполнения технологических и контрольных
операций. Время подготовительно-заключительной работы, время наладки оборудования,
также входят в структуру цикла, также подлежит уменьшению. Налаживание
оборудование, как правило, необходимо выполнять в нерабочие смены, в обеденные и
другие перерывы. В заводской практике успешно применяют меры по сокращению
периода выполнения этой работы, например, внедрение групповой обработки
деталей, типовых и универсальных настроек. Продолжительность естественных процессов
уменьшается за счет замены их соответствующими технологическими операциями.
Например, естественная сушка некоторых окрашенных деталей может быть заменено
индукционным сушкой в поле токов высокой частоты со значительным (в 5-7 раз)
ускорением процесса. Вместо естественного старения отливок ответственных
деталей, что длится 10-15 суток и более, во многих случаях может быть
применено искусственное старение в термических печах в течение нескольких часов.
Время межоперационных перерывов может быть
значительно уменьшено в результате перехода от последовательного к последовательно-параллельного
и далее до параллельного вида движений предметов труда. Его также может быть
сокращены за счет организации цехов и участков на основе предметной
специализации. Обеспечивая территориальное сближение различных стадий производства,
предметная форма построения цехов и участков позволяет значительно упростить
внутризаводские и внутрицеховые маршруты движения и тем самым уменьшить время,
затрачиваемое на межцеховые и внутрицеховые передачи. Наконец, величину
міжзмінних перерывов может быть снижена даже в рамках принятого режима работы
предприятия, цеха, участка. Например, организация круглосуточной (трехсменного)
работы по выпуску ведущих деталей и изделий, имеющих длительный цикл обработки
и определяют продолжительность цикла изделия. Чтобы вскрыть резервы сокращения
производственного цикла (как трудовых процессов, так и перерывов), на практике
фотографируют производственный цикл. Анализируя фотографии, можно выявить резервы
сокращение продолжительности производственного цикла за каждым его элементом.
Производственный цикл сложного
(сборочного) процесса представляет собой общую продолжительность комплекса координированных
во времени простых процессов, входящих в сложный процесс изготовления изделия или
его партий.
В условиях машиностроительного производства
наиболее характерными примерами сложного процесса являются процессы создания машины,
металлорежущего станка или узлов, блоков, мелких единиц, из которых они
состоят.
Производственный цикл сложного процесса
включает производственные циклы изготовления всех деталей, сборки всех сборочных
единиц, генеральная сборка изделия, контроль, регулирование и наладка. В
сложном производственном процессе могут использоваться все рассмотренные виды движения
предметов труда по операциям: последовательный, последовательно-параллельный и
параллельный. Для условий включения единичного производства в единый цикл, как
правило, необходимы не только процессы изготовления и сборки, но и процессы
проектирования изделия и подготовки его производства.
Сложный производственный процесс конечно
состоит из большого количества сборочных, монтажных,
регулировочно-наладочных операций, операций простых процессов, поэтому
определение и оптимизация производственного цикла требуют не только больших затрат
времени, но и нередко применение ЭВМ для выполнения расчетов. Построение
сложного производственного процесса во времени осуществляется для того, чтобы определить
продолжительность производственного цикла, координировать выполнение отдельных простых процессов,
получить необходимую информацию для оперативно-календарного планирования и
расчета операции запуска-выпуска предметов труда. Целью координации
производственных процессов, составляющих сложный процесс, является обеспечение
комплектности и бесперебойности хода производства при полной загрузке
оборудования, рабочих мест и рабочих.
Структура производственного цикла
сложного процесса определяется составом операций и связей между ними. Состав
операций зависит от номенклатуры деталей, сборочных единиц и технологических
процессов их изготовления. Взаимосвязь операций и процессов предопределяется
віяловою схемой сборки изделия и технологией его изготовления. Веерная схема
сборка изделия показывает, какие узлы, підвузли или мелкие сборочные единицы
можно изготавливать параллельно независимо друг от друга, а какие - только
последовательно.
Расчет длительности производственного
цикла сложного процесса необходимо вести в такой последовательности:
- определить размер партии
изделий;
- вычислить удобство ритма,
планируется;
- рассчитать число партий,
запускаемых в течение планового периода;
- определить время операционного
цикла партии изделий;
- рассчитать продолжительность
операционного цикла партии изделий по сборочным единицам;
- определить количество рабочих
мест, необходимых для изготовления изделий;
- построить цикловой график
сборки изделий без учета загрузки рабочих мест;
- закрепить операции за рабочими
местами;
- составить стандарт-план сборки
изделий;
- построить уточненный цикловой
график с учетом загрузки рабочих мест;
- определить продолжительность
производственного цикла и опережения запуска-выпуска по сборочными единицами и
деталями.
За решение вопроса о размерах
партии необходимо исходить из экономически оптимального размера. Работа большими
партиями позволяет реализовать принципы партионности, что обеспечивает:
а) возможность применения более
производительного процесса, что снижает затраты на изготовление изделий;
б) уменьшение подготовительно-заключительного
времени, приходящаяся на единицу продукции;
в) сокращение потерь времени
рабочих-сборщиков на освоение приемов работы (приспособления к работе);
г) упрощение календарного
планирование производства.
Эти факторы способствуют зарастанию
производительности труда рабочих и снижению себестоимости продукции.
Однако в единичном и серийном
производствах, где за каждым рабочим местом закрепляется выполнение нескольких
операций и где преобладает последовательный вид движения предметов труда, с ростом
размера партии повышается степень нарушения принципа непрерывности, поскольку
увеличивается время пролеживания каждой сборочной единицы, то есть растет
продолжительность производственного цикла изготовления партии изделий, количество сборочных
единиц, находящихся в наробці и на сохранении (незавершенное производство).
Кроме того, возрастает потребность в площадях для хранения изделий и материальных
ценностей, одновременно необходимых для производства.
ЭТИ и противоположные факторы, связанные с
реализацией одного принципа (партионности) и нарушением другого
(непрерывности), требуют определения такого размера партии, за которого
сочетание экономии от реализации первого принципа и потерь от нарушения
другой, были бы наиболее рациональными с экономической точки зрения. Такой размер
партии принято называть экономически оптимальным.
Определение оптимального размера
партии изделий является одним из важнейших календарно-плановых нормативов по
организации серийного производства, потому что все другие календарно-плановые
нормативы устанавливаются на партию предметов труда.
Формул для расчета оптимального
размера партий изделий, основанных на сопоставлении экономии и потерь,
предложено различными авторами много. Однако из-за большой трудоемкости
расчетов эти формулы не получили широкого применения. На промышленных
предприятиях обычно используют упрощенный метод расчета, исходя из
приемлемого коэффициента потерь рабочего времени на переналадку и текущий
ремонт рабочих мест (αппр). Как правило, величину этого
коэффициента принимают в пределах от 0,02 для крупносерийного и до 0,1 - для
мелкосерийного и единичного производств (или от 2 до 10 %). Задаваясь для
определенных производственных условий величиной данного коэффициента аппр, можно
определить количество изделий в партии по формуле
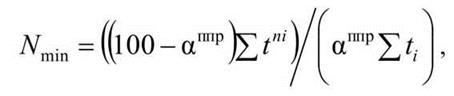
где
tni- подготовительно-заключительное время за
операциям технологического процесса.
Полученный результат рассматривается как
минимальная величина партии изделий. За максимальную величину можно принять
месячную программу выпуска изделий (сборочных единиц). Таким образом, в
результате проведенных расчетов устанавливаем пределы нормального размера партии
изделий:
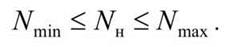
Предельные размеры партии изделий
корректируются, исходя из минимального размера. Корректировка начинается со
установление удобного для планирования ритма (Вг) - период дежурства
партий изделий. Если в месяце 20 рабочих дней, то удобными для планирования
ритмами будут 20, 10, 5, 4, 2 и 1; если в месяце 21 день, то такими ритмами
будут 21, 7, 3 и 1; если 22 дня, то 22, 11, 2 и 1.
Период чередования партий изделий
рассчитывают по формуле

где
Др - количество рабочих дней в месяце.
Если по расчету получается дробное
число, то из ряда удобных для планирования ритмов выбирают ближайшее целое число,
то есть принятое значение периода дежурства.
Далее в соответствии с принятым
периода дежурства корректируем размер партии изделий по формуле

Нормальный размер партии изделий должен
быть кратным месячной программе выпуска (запуска) изделий.
Число партий в месяц определяется
по формуле
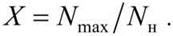
Длительность операционного цикла партии
изделий по каждой операции рассчитывается по формуле

Длительность операционного цикла партии
изделий по сборочным единицам определяется по формуле
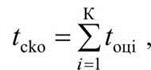
где
К - количество операций, входящих в сборочную единицу.
Необходимое число рабочих мест для
сборки изделий рассчитывается по формуле
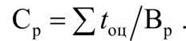
Если расчетное значение количества
рабочих мест является дробной величиной, то необходимо его скорректировать в сторону
увеличение или уменьшение, с учетом того, что каждое рабочее место может быть
перегружено не более чем на 5 %.
Необходимое количество рабочих
определяется по формуле

где
Ксн - коэффициент, учитывающий учетную численность (конечно
принимается равным 1,1).
Построение циклового графика сборки
изделия без учета загрузки рабочих мест ведется на основе веерной схемы
составление и продолжительности циклов сборки каждой i-той операции и каждой
сборочной единицы. Как правило, такой график строится в порядке, обратном
к ходу технологического процесса, начиная с последней операции, с учетом того,
к какой операции поставляются сборочные единицы. Продолжительность этого цикла
графика будет минимальной. Однако условия производства и ограниченные ресурсы требуют
выполнение определенных работ последовательно, на том самом рабочем месте, стенде.
Все это приводит к изменениям в цикловому графику и, как правило, к смещению запуска
на более ранние сроки, а как следствие - к увеличению продолжительности цикла.
Для достижения равномерности
загрузки рабочих мест и рабочих-сборщиков необходимо закрепить
операции за рабочими местами. С этой целью на каждое рабочее место набирается
объем работ, продолжительность операционного цикла которых не должна превышать пропускной
способности рабочих мест в течение принятого периода дежурства.
Построение стандарт-плана составление
изделия (циклового графика с учетом загрузки рабочих мест). График
строится без учета загрузки рабочих мест и данных о закреплении
операций за рабочими местами. При этом периоды выполнения отдельных циклов
операций графика должны проецироваться на соответствующие рабочие места на цикловому
графика сборки изделия без учета загрузки рабочих мест. В этом случае
сохраняется длительность производственного
цикла на графике, построенном
без учета загрузки рабочих мест. Однако не всегда удается это осуществить.
Сдвиги работ на более ранний период времени повлечет увеличение продолжительности
производственного цикла и появление пролеживания сборочных единиц. На этом же графике
необходимо привести производство второй, третьей и последующих партий изделий до тех пор,
пока не заполнится полностью один период чередования партий изделий. Заполненный
период дежурства и представляет собой стандарт-план, потому что именно здесь показаны
стандартные, повторяющиеся сроки проведения отдельных операций сложения каждым
рабочим-сборщиком.
Далее происходит построение
уточненного циклового графика сборки изделия и определение фактической продолжительности
производственного цикла, что конечно немного больше минимальной, поскольку выполнение
некоторых операций сдвинуто на более ранние сроки.
Уточненный график сборки изделий
строится на основе уже построенных стандарт-планов сборки изделия без учета
и с учетом загрузки рабочих мест, времени сдвига запуска соответствующих
сборочных единиц, и по этому графику определяется фактическая продолжительность
производственного цикла сборки партии изделий.