РАЗДЕЛ III
ОРГАНИЗАЦИЯ ДЕЯТЕЛЬНОСТИ ПРЕДПРИЯТИЯ
ТЕМА 19
ОРГАНИЗАЦИЯ ПРОИЗВОДСТВА
19.4. Общая характеристика методов
организации производства
Методы организации производства
представляют собой совокупность способов, приемов и правил рационального сочетания
основных элементов производственного процесса в пространстве и времени на стадиях
функционирования, проектирования и совершенствования организации производства.
Метод организации индивидуального
производства. Этот метод используется в условиях единичного выпуска продукции
или производства ее малыми сериями и предполагает:
- отсутствие специализации на
рабочих местах;
- применение
широкоуніверсального оборудования, размещение его группами по функциональному
назначению;
- последовательное перемещение деталей
с операции на операцию партиями.
Условия обслуживания рабочих мест
отличаются тем, что рабочие почти постоянно пользуются одним набором
инструментов и небольшим количеством универсальных приспособлений, нужна лишь
периодическая замена инструмента, затупился или износился. В противовес этому
подвозка деталей к рабочим местам и отправка деталей по выдаче нового
задача или за прием законченной работы происходит несколько раз в течение
изменения. Поэтому возникает необходимость гибкой организации транспортного
обслуживание рабочих мест.
Рассмотрим основные стадии
организации индивидуального производства:
Этап 1. Определение типов и количества
станков, необходимых для выполнения заданной производственной программы. По организации
индивидуального производства точно установить номенклатуру продукции,
выпускается, трудно, поэтому допустимы приближенные расчеты необходимого количества
станков. В основу расчета берутся следующие показатели: съем продукции с
единицы оборудования; количество станко-часов, необходимое для обработки
комплекса деталей на одно изделие. Точность укрупненных расчетов зависит от
того, насколько правильно определены значения этих показателей. Расчетная
количество станков определяется по формуле
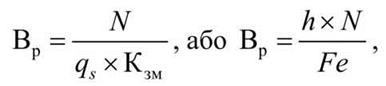
где
N - годовой объем выпуска продукции, пит.;
qs - съем продукции с единицы
оборудование, пит.;
Кзм - коэффициент
сменности работы рассматриваемой группы оборудования; h - количество станко-часов,
необходимая для обработки комплекса деталей на одно изделие;
Fe - эффективный фонд рабочего времени
одного станка рассматриваемой группы, ч.
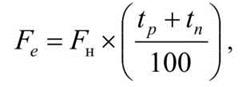
где
FH - нормативные затраты времени на ремонт
оборудования, % к номинальному фонду;
tp - нормативные затраты времени на
наладку, переналадку оборудования, % к номинальному фонду;
tn - номинальный фонд времени работы
станка, ч.
Номинальный фонд времени работы
оборудования зависит от количества календарных и нерабочих дней в году,
принятого режима сменности за сутки и определяется по формуле
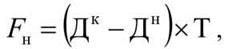
где
Дк - количество календарных дней в году;
Дн - количество нерабочих
дней в году;
Т - среднее количество часов работы
станка за сутки, согласно принятого режима сменности.
Принятое количество станков по
каждой группе оборудования устанавливается путем округления полученного значения
до целого так, чтобы общее количество станков не выходила за пределы принятого
их числа.
Коэффициент загрузки оборудования
определяется отношением расчетного количества станков к принятому.
Этап 2. Согласование пропускной
способности отдельных участков мощности. Производственная мощность участка, оснащенного
однотипным оборудованием, определяется так:

где
Впр - принятое количество станков, шт.;
Кнзм - нормативный
коэффициент сменности работы оборудования;
FH - номинальный фонд времени работы
оборудования, ч.;
К - коэффициент выполнения норм, достигнутый в базисном
году по участку (цеху);
Стр - плановое задание по
снижение трудоемкости, нормо-часа.
Нормативный коэффициент сменности
работы оборудования определяется, исходя из расчета загрузки
установленного оборудования, как правило, при двухсменном режиме работы и
нормативном коэффициенте, учитывающий время пребывания станка в ремонте.
Взаимосвязь отдельных участков по
мощностью определяется по формуле
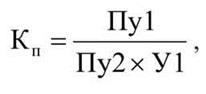
где
Кп - коэффициент сопряженности участков по мощности;
Пу1, Пу2 - мощности сравниваемых участков (продукция 1-й
участка используется для изготовления единицы продукции 2-го участка);
У1 - удельный расход продукции 1-го
подразделения.
Этап 3. Организация рабочего места.
Особенности организации и обслуживания рабочих мест состоит в налаживании
станка перед началом работы, а также установке инструмента на рабочих местах,
что осуществляется самими рабочими. Рабочие места при этом должны быть оснащены
всем необходимым для обеспечения непрерывной работы, а транспортировка деталей
должна осуществляться без задержек, не создавая на рабочих местах лишнего запаса
заготовок.
Этап 4. Разработка планировки участков.
Для индивидуального производства характерно планирование участков по видам работ.
В этом случае создаются участки однородных станков.
Последовательность расположения участков
на площади определяется маршрутом обработки большинства типов деталей и имеет
обеспечивать перемещение деталей до конечного этапа изготовления изделия.
Организации производства поточным
методом. Применение этого метода обеспечивает изготовление изделий одного
наименование или типового ряда и требует совокупности специальных организационных
мероприятий построения производственного процесса: расположение рабочих мест по ходу
технологического процесса; специализацию каждого рабочего места для выполнения
одной из операций; передачи предметов труда с операции на операцию поштучно и
мелкими партиями сразу же после окончания обработки; ритмичность выпуска,
синхронности операций; детальной проработки организации технического
обслуживание рабочих мест.