РАЗДЕЛ III
ОРГАНИЗАЦИЯ ДЕЯТЕЛЬНОСТИ ПРЕДПРИЯТИЯ
ТЕМА 19
ОРГАНИЗАЦИЯ ПРОИЗВОДСТВА
19.3. Форма
организации производства как характеристика пространственно-временной структуры производственного
процесса
Форма организации производства представляет
собой определенное сочетание во времени и в пространстве элементов производственного процесса
соответствующего уровня его интеграции, которые отражаются в системе устойчивых связей.
Различные производственные структуры,
построенные во времени и пространстве, образуют совокупность основных форм организации
производства.
Временная структура форм организации
производства определяется составом элементов производственного процесса и порядком их
взаимодействия во времени. По виду временной структуры различают формы организации с
последовательной, параллельной и параллельно-последовательной передачей предметов труда в
производстве.
Форма организации производства с
последовательной передачей предметов труда представляет собой такое сочетание
элементов производственного процесса, при котором обеспечивается движение обрабатываемых изделий
по всем производственным участкам партиями произвольной величины. Предметы труда на
каждую последующую операцию передаются только после окончания обработки всей
партии на предыдущей операции. Эта форма является наиболее гибкой по отношению к изменениям,
возникают в производственной программе, позволяет достаточно полно использовать
оборудования, что дает возможность снизить затраты на его приобретение. Недостаток
формы организации с последовательной передачей предметов труда заключается в относительно
большой длительности производственного цикла, потому что каждая деталь перед выполнением
следующей операции пролеживается в ожидании обработки всей партии.
Форма организации производства с
параллельной передачей предметов труда основана на таком сочетании элементов
производственного процесса, что позволяет запускать, обрабатывать и передавать предметы
труда с операции на операцию поштучно и без ожидания. Такая организация
производственного процесса приводит к уменьшению количества деталей, находящихся в
обработке, сокращение потребностей в площадях, необходимых для складирования и проходов.
Недостаток формы организации с параллельной передачей предметов труда заключается в
возможных простоях оборудования (рабочих мест), возникающих вследствие
различий в длительности операций.
Форма организации производства с параллельно-последовательной
передачей предметов труда является промежуточной между последовательной и параллельной формами и
частично устраняет присущие им недостатки. Изделия с операции на операцию передаются
транспортными партиями. При этом обеспечиваются непрерывность использования оборудования
и рабочей силы, частично параллельное прохождение партии деталей по операциям
технологического процесса. Пространственная структура форм организации производства
определяется количеством технологического оборудования, сосредоточенного на рабочем
площадке, и расположением их относительно направления движения предметов труда и
окружающего пространства.
В зависимости от количества технологического
оборудования (рабочих мест) различают одноланкову производственную систему и
соответствующую ей структуру обособленного рабочего места и многозвенную систему с
цеховой, линейной или ячеечной структурой. Возможные варианты пространственной
структуры представлено на рис. 19.2.
Цеховая пространственная структура
характеризуется созданием участков, на которых оборудование (рабочие места)
расположено параллельно потоку заготовок, что предполагает их специализацию по
признаку технологической однородности. В этом случае партия деталей, что
поступает на участок, направляется на одно из свободных рабочих мест, где
проходит необходимый цикл обработки, после чего передается на другой участок (в
цех).
На участке с линейной пространственной
структурой рабочие места (оборудование) располагаются по ходу технологического
процесса, и партия деталей, обрабатываемая на участке, передается с одного
рабочего места на другое в прямой последовательности.
Очаговая пространственная структура
сочетает признаки линейной и цеховой. Комбинация пространственной и временной структуры
производственного процесса определенного уровня интеграции частичных процессов обусловливает
различные формы организации производства: технологическую, предметную, прямоточную, точечную,
интегрированную. Рассмотрим характерные черты каждой из них.
Технологическая форма организации
характеризуется цеховой структурой с последовательной передачей предметов труда.
Такая форма организации распространена на
машиностроительных предприятиях, поскольку обеспечивает максимальную загрузку
оборудования в условиях мелкого несерийного производства и приспособлена к частым
изменений в технологическом производственном процессе.
В то же время применение
технологической формы имеет ряд негативных последствий. Большое количество деталей и
их многократное перемещение в процессе обработки приводят к росту объема
незавершенного производства и увеличение числа пунктов промежуточного
складирования.
Значительную часть производственного цикла
составляют потери времени, обусловлено сложными связями между участками.
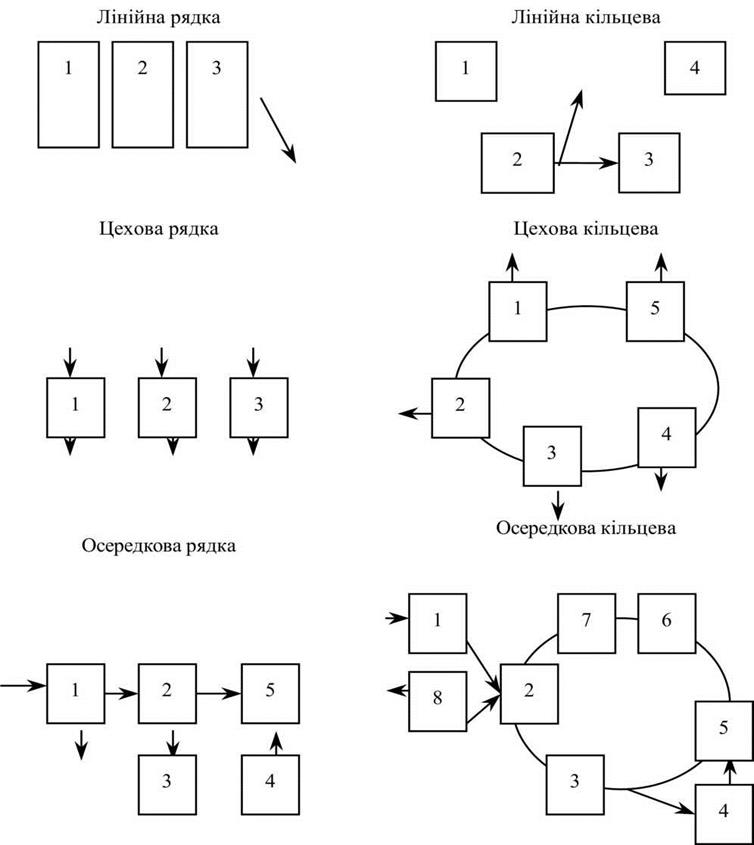
Рис. 19.2. Варианты пространственной
структуры взаимосвязи рабочих мест
Предметная форма организации
производства имеет осередковану структуру с параллельно-последовательной (последовательной)
передачей предметов труда в производстве. На предметной участке устанавливается,
как правило, все оборудование, необходимое для обработки группы деталей с начала
и до конца технологического процесса. Если технологический цикл обработки
замыкается в границах участка, он называется предметно-замкнутым. Предметная
построение участков обеспечивает прямоточність и уменьшение длительности производственного
цикла изготовления деталей. По сравнению с технологической формой организации
предметная позволяет снизить общие затраты на транспортировку деталей, потребность
в производственной площади на единицу продукции. Вместе с тем данная форма имеет и недостатки.
Главный из них заключается в том, что за определение состава оборудования,
устанавливается на участке, на первый план выдвигается необходимость выполнения
определенных видов обработки, что не всегда обеспечивает полную загрузку оборудования.
Кроме того, расширение номенклатуры выпускаемой продукции, ее обновление
обусловливают потребность в периодическом перепланировке производственных участков, изменении
структуры парка оборудования.
Прямоточная форма организации
производства характеризуется линейной структурой с передачей поштучною
предметов труда. Такая форма обеспечивает реализацию ряда принципов организации:
специализации, прямоточности, непрерывности, параллельности. Применение
прямоточної формы приводит к сокращению длительности цикла, более эффективного
использования рабочей силы за счет большей специализации труда, уменьшение
объема незавершенного производства.
За точечной формы организации
производства работа полностью выполняется на одном рабочем месте. Изделие
изготавливается там, где находится его основная часть. Примером может быть
сборки изделия с перемещением рабочего вокруг него. Организация точечного
производства имеет ряд преимуществ: обеспечиваются возможность частых изменений
конструкции изделий и последовательности обработки, возможность изготовления изделий
разнообразной номенклатуры в количестве, обусловленной потребностями производства;
снижаются расходы, связанные с изменением размещении оборудования; повышается
гибкость производства.
Интегральная форма организации
производства предполагает объединение основных и вспомогательных операций в единый
интегрированный производственный процесс с очаговой или линейной структурой по
последовательной, параллельной или параллельно-последовательной передаче предметов труда в
производстве. В отличие от существующей практики раздельного проектирования процессов
складирования, транспортировки, управления, обработки, участках с
интегрированной формой организации нужно увязывать эти частичные процессы в
единый производственный процесс. Это достигается объединением всех рабочих мест по
помощью автоматического транспортно-складского комплекса, который представляет собой
совокупность взаимосвязанных, автоматических и складских устройств, средств
вычислительной техники, предназначенных для организации хранения и перемещения
предметов труда между отдельными рабочими местами.
Управление производственным процессом
осуществляется с помощью ЭВМ, что обеспечивает функционирование всех элементов
производственного процесса на участке, по такой схеме: поиск необходимой заготовки на
складе - транспортировка заготовки к станку - обработка - возвращение детали
на состав. Для компенсации отклонений во времени по транспортировки и обработки деталей
на отдельных рабочих местах создаются буферные склады межоперационных и страховых
наработок.
Создание интегрированных производственных
участков связано с относительно высокими единовременными затратами, вызванными
интеграцией и автоматизацией производственного процесса. Экономический эффект при
переходе к интегрированной форме организации производства достигается за счет
сокращение производственного цикла изготовления деталей, увеличения времени загрузки
станков, улучшения регулирования и контроля процессов производства.
В зависимости от способности к
переналадки на выпуск новых изделий перечисленные выше формы организации
условно можно разделить на гибкие (переналагоджувані) и твердые (не
переналагоджувані).
Твердые формы организации производства
предполагают обработки деталей одного наименования. Изменение в номенклатуре
выпускаемой продукции и переход на выпуск конструктивно новой серии
изделий вызывают необходимость перепланировки участка, замены оборудования и
оснастки. К числу твердых принадлежит поточная форма организации.
Гибкие формы организации производства
позволяют обеспечивать переход на выпуск новых изделий без изменения состава
компонентов производственного процесса за незначительных затрат труда и времени.
Наибольшее распространение на
машиностроительных предприятиях в настоящее время получили такие формы организации
производства, как гибкое точечное производство, гибкая предметная и поточная формы.
Гибкое точечное производство предполагает
пространственную структуру обособленного рабочего места без дальнейшей передачи
предметов труда в процессе производства. Деталь полностью обрабатывается на одной
позиции. Приспособленность к выпуску новых изделий осуществляется за счет изменения
рабочего состояния системы.
Гибкая предметная форма организации
производства характеризуется возможностью автоматической обработки деталей в
пределах определенной номенклатуры без перерыва на переналадку. Переход к
выпуска новых изделий осуществляется путем переналадки технических средств,
перепрограммирование системы управления. Гибкая предметная форма охватывает область
последовательной и параллельно-последовательной передаче предметов труда в сочетании с
комбинированной пространственной структурой.
Гибкая поточная форма организации
производства характеризуется быстрым переналадкой на обработку новых
деталей в пределах заданной номенклатуры путем замены инструментальной оснастки и
приспособлений, перепрограммирования системы управления. Она основана на рядному
расположении оборудования, что строго соответствует технологическому процессу с
поштучною передачей предметов труда.
Под влиянием научно-технического
прогресса на технику и технологию в машиностроении происходят существенные изменения,
обусловленные механизацией и автоматизацией производственных процессов. Это означает
объективные предпосылки развития новых форм организации производства. Одной из
таких форм, получившей применение при внедрении средств гибкой
автоматизации в производственный процесс, является блочно-модульная форма организации
производства.
Создание производства с
блочно-модульной формой организации осуществляется путем концентрации на участке
всего комплекса технологического оборудования, необходимого для непрерывного
производства ограниченной номенклатуры изделий, и наделение группы рабочих при
выпуска конечной продукции с передачей им части планирования и управления
производством на участке. Экономической основой создания таких производств
выступают коллективные формы организации труда. Работа в этом случае строится
на принципах самоуправления и коллективной ответственности за результаты труда.
Основными требованиями, предъявляемыми к организации процесса производства и труда,
в этом случае есть:
а) создание автономной системы
технического и инструментального обслуживания производства;
б) достижение непрерывности
процесса производства на основе расчета рациональной потребности в ресурсах с
указанием интервалов и сроков поставок;
в) обеспечение соответствия по
мощности механообрабатывающих и сборочных подразделений;
г) учет установленных норм
управляемости при определении количества работающих;
д) подбор группы работающих с
учетом полной взаимозаменяемости.
Исходя из указанных требований,
эффективное производство возможно
только
при условии комплексного решения вопросов организации труда, производства и
управления. Переход к блочно-модульной формы организации производства
проводится в несколько этапов. На этапе предпроектного обследования принимается
решение о целесообразности создания подразделений с блочно-модульной формой
организации на данных производственных уровнях. Производится анализ
конструктивно-технологической однородности продукции и дается оценка возможности
комплектации групп деталей для обработки в рамках производственного отделения. Потом
определяется возможность концентрации всего комплекса технологических операций по
выпуска группы деталей на одном участке, устанавливается количество рабочих мест,
приспособленных для внедрения групповой обработки деталей, определяются состав и
содержание основных требований к организации процесса производства и труда исходя из
намеченного степени автоматизации на стадии структурного проектирования
определяются состав и взаимосвязи основных компонентов производственного процесса.
На стадии организационно-экономического
проектирование сочетаются технические и организационные решения, намечаются пути
реализации принципов коллективного подряда и самоуправления в автономных
бригадах.
Вторым направлением развития форм
организации производства является переход на составление стендовым методом сложных
агрегатов, отказ от конвейерной системы сборки путем организации
мініпотоку. Весь процесс сборки разделен на несколько больших этапов. На
каждом этапе действуют рабочие группы по 15-25 сборщиков. Бригада располагается
вдоль наружных стен, внутри расположены кассы с необходимыми на данном этапе
составление деталями. Машины состоят на самодвижущихся платформах, передвигаясь
по укрупненному операциях в рамках данного этапа. Каждый рабочий вполне завершает
свою операцию. Принцип потока при такой системе сборки вполне сохраняется,
поскольку общее количество одинаковых параллельно работающих стендов такая, что
поддерживается средний заданный такт потока. За движением платформ с машинами,
собираются, с одного этапа подготовки на другой следит диспетчерская служба по
помощью ЭВМ.
Другим решением организации
поточного производства является сохранение конвейерной системы с включением в нее
подготовительных операций. В таком случае сборщики, по своему усмотрению,
работают то на основных, то на подготовительных операциях. Указанные подходы в
развития поточной формы организации производства не только обеспечивают
рост производительности труда и повышение качества, но и дают сборщикам
чувство удовлетворения от работы, исключают монотонность труда.
Организация производственного процесса в
времени характеризуется способами сочетания операций технологического процесса,
структурой и длительностью производственного цикла. Производственный цикл - это интервал от
начала до окончания процесса изготовления продукции, т.е. время, в течение которого
запущенные в производство предметы труда превращаются в готовую продукцию.
Он вычисляется для одного изделия
или для определенного количества изделий, изготавливаемых одновременно. Производственный цикл
является важным календарно-плановым нормативом организации производственного процесса в
времени. Исходя из его продолжительности, определяют срок запуска продукции в
производство, составляют календарные планы ее изготовления на всех стадиях
производственного процесса, согласовывают работу смежных подразделений (участков, цехов).
На основании производственного цикла вычисляют величину незавершенного производства -
важный элемент оборотных средств предприятия.
Из него видно, что производственный цикл
состоит из производственного времени и перерывов. Время производства особых объяснений не
нуждается. Время перерывов включает перерывы в рабочее время, то есть тогда, когда
предприятие работает, и нерабочее время, который определяется режимом работы
(выходные, праздничные дни, перерывы между рабочими сменами).
Перерывы в рабочее время подразделяются на
перерывы партионности и ожидания. Перерывы партионности возникают тогда, когда
предметы труда обрабатываются партиями. Партия предметов - это определенное количество
одинаковых предметов, которые обрабатываются на каждой операции непрерывно с
однократной затратой подготовительно-заключительного времени. Предметы партии обрабатываются
не одновременно, а по одному или несколько сразу. Каждый предмет труда ждет
сначала своей очереди на обработку, а затем - конца обработки всей партии. Перерыва
партионная исчисляются не отдельно, а вместе с продолжительностью технологических
операций, образуя технологический цикл. Перерывы ожидания возникают вследствие
асинхронности операций производственного процесса: предметы труда негде обрабатывать,
потому что рабочие места заняты другими операциями. Перерывы ожидания возникают также
тогда, когда детали, входящие в один комплект, изготавливаются в разное время.
Конкретная структура производственного
цикла зависит от особенностей продукции, технологических процессов ее
изготовления, типа производства и других факторов. В непрерывных
производствах (химическом, металлургическом и т. п.) наибольшую долю в производственном
цикле занимает время производства. В дискретных производствах существенную долю
производственного цикла составляют перерыва. Особенно длительными есть перерывы в единичном
производстве, меньше - в серийном и минимальными - в массовом.
Производственный цикл можно вычислять как
для отдельных предметов (деталей, узлов, изделий), так и для целых партий.
Определение цикла осуществляется за составляющими его элементами. Для изделий из
длительным циклом величина последнего исчисляется в календарных днях, в этом
случае учитываются все перерывы. Короткие циклы (до 5 дней) исчисляются в рабочих
днях без учета выходных.
Основной составляющей производственного цикла
является продолжительность технологических операций, которая составляет технологический цикл.
Технологический цикл обработки партии предметов на одной операции равна
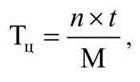
где Тц -
технологический цикл в единицах времени, как правило, в минутах; n - количество предметов в партии;
t - продолжительность обработки одного
предмета;
М - количество рабочих мест, на которых
выполняется операция.
Технологический цикл партии предметов,
которые обрабатываются на нескольких
операциях, зависит
также от того, как сочетается выполнения операций над предметами партии.
Существуют три способа сочетания операций технологического процесса (три способа
передачи предметов): последовательный, параллельный, параллельно-последовательный.
Последовательное сочетание операций
заключается в том, что следующая операция начинается только после окончания
обработки всех предметов партии на предыдущей операции. Партия предметов
передается с операции на операцию целиком. Технологический цикл за такого
сочетание операций вычисляется по формуле
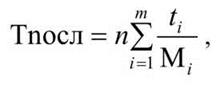
где m - количество операций технологического
процесса (i = 1,2...m).
Последовательное сочетание операций является
достаточно простым по своей организации, облегчает оперативное планирование и учет.
Но оно требует длительного цикла, ибо каждый предмет лежит, дожидаясь обработки
всей партии. Последовательное сочетание операций применяется в единичном и
серийном производствах.
Параллельное сочетание операций
характеризуется тем, что каждый предмет труда после окончания предыдущей
операции сразу передается на следующую операцию и обрабатывается. Следовательно
предметы одной партии изготавливаются параллельно на всех операциях.
Малогабаритные нетрудоемкие предметы могут передаваться не поштучно, а
транспортными (передаточными) партиями - nm. При поштучной передаче nm = 1.
При параллельном соединении
продолжительность операций не одинакова и не кратна, то есть, когда они не
синхронизированы, то на всех операциях, кроме операции с максимальной продолжительностью,
возникают перерывы в работе. Перерыва ликвидируются при условии синхронизации
операции, когда
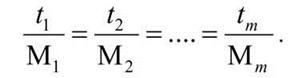
Параллельное сочетание операций
применяется в массовом и крупносерийном производствах.
Параллельно-последовательное сочетание
операций, которое еще называют смешанным, отличающийся тем, что обработка предметов
труда на последующей операции начинается до окончания обработки всей партии
на предыдущий, но при условии, чтобы партия обрабатывалась на каждой операции
беспрерывно.
Технологический цикл по
параллельно-последовательного сочетания операций короче цикл последовательного сочетания
на время параллельного выполнения смежных операций т, то есть:
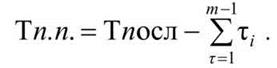
Время параллельного выполнения смежных
операций равна произведению количества деталей без одной транспортной партии и
продолжительности меньшей операции. Если последнюю обозначить (АМ)К, то в общем виде
для любой пары смежных операций выражение будет таким:

По параллельно-последовательного сочетания
операций технологический цикл более длительный от цикла за параллельного и меньше чем
цикл за последовательного сочетания операций. Применяется этот метод, когда предметы
обрабатывают большими партиями, что соответствует условиям крупносерийного производства.
Для расчета производственного цикла
обработки партии предметов наряду с технологическим циклом надо определить другие
его элементы. Продолжительность естественных процессов берется в соответствии с требованиями
технологии, время выполнения вспомогательных операций и операционных перерывов
определяется по определенным нормативам или по опыту. Тогда производственный цикл
обработки партии предметов в календарных днях может быть вычислен, например,
для последовательного сочетания операций по формуле

где
kкал - коэффициент календарності;
kзм - количество смен за сутки;
tсм - продолжительность смены в часах;
tпр - длительность естественных, вспомогательных
операций, которые не перекрываются, мин.;
tg - продолжительность средней
міжопераційної перерывы (ожидание), мин.
Коэффициент календарності - это
отношение количества календарных дней к количеству рабочих дней в определенном
периоде (месяце, квартале, году).
Пространственная организация производственного
процесса предполагает размещение рабочих мест и их групп (участков, цехов) на
территории предприятия и обеспечение передвижения предметов труда по операциям
за кратчайшими маршрутами. Сочетание этих двух аспектов построения производственного
процесса осуществляется применением соответствующего метода организации производства.
Выделяют два метода организации производства: непоточный и потоковый.
Непоточном производству свойственны
такие признаки: на рабочих местах обрабатываются разные по конструкции и технологии
изготовления предметы труда, ибо количество каждого из них является небольшим и недостаточным
для нормальной загрузки оборудования; рабочие места размещаются по
однотипными технологическими группами без определенной связи с последовательностью
выполнения операций, например, группы токарных, фрезерных, сверлильных и других
станков; предметы труда перемещаются в процессе обработки сложными
маршрутам, вследствие чего являются большие перерывы между операциями. После отдельных
операций предметы труда часто поступают на промежуточные склады и ждут
освобождения рабочего места для выполнения следующей операции.
Непоточный метод применяется
преимущественно в единичном и серийном производствах. В зависимости от номенклатуры
изделий и их количества он может иметь различные модификации. В условиях единичного
производства непоточный метод осуществляется преимущественно в форме единично-технологического,
когда отдельные предметы труда единицами или небольшими партиями, которые не
повторяются, проходят обработку в соответствии с приведенным выше порядком. В серийном
производстве этот метод набирает формы партионно-технологического или
предметно-группового.
Партионно-технологический метод
отличается от единично-технологического тем, что предметы труда проходят
обработку партиями, которые периодически повторяются. Партия предметов труда является
важным календарно-плановым нормативом организации партионного производства, ее
величина существенно влияет на его эффективность, причем это влияние не
однозначный. С одной стороны, увеличение величины партии обеспечивает уменьшение
количества переналагоджувань оборудования, вследствие чего улучшается его
использования, уменьшаются затраты на подготовительно-заключительные работы
(переналагоджування, получение и сдача работы ознакомление с технической
документацией и т. п.). Кроме этого, упрощается оперативное планирование и учет
производства. С другой стороны, обработка предметов большими партиями увеличивает
объем незавершенного производства, требует больших
складских помещений, а это приводит к дополнительным расходам.
Уменьшение величины партии предметов
оказывает на эффективность производства противоположное влияние. Поэтому очень важно
определить величину оптимальной партии. Оптимальной является такая партия предметов,
когда общие затраты на ее изготовление будут минимальными. Она исчисляется
в процессе оперативного управления производством.
Единично - и партионно-технологические
методы производства организационно являются достаточно сложными, их недостатки немного
ослабляются применением предметно-группового метода. Суть последнего заключается
в том, что вся совокупность предметов труда разделяется на технологически
подобные группы. Обработки предметов каждой группы осуществляется по приблизительно
одинаковой технологии и требует одинакового оборудования. Это дает возможность
создавать для обработки предметов группы предметно специализированные участки,
повышать уровень механизации и автоматизации производства. Предметно-групповые
методы создают предпосылки для перехода к поточному производству.
Оборудования в непоточном
производстве является преимущественно универсальным, а рабочие - универсалами высокой
квалификации. Высокий уровень специализации оборудования, как отмечалось,
используется в случае применения предметно-групповых методов, поскольку по
в определенной предметно-специализированным участком закрепляется меньшее количество
предмето-операций.
Для непоточных методов характерно
последовательное (редко - последовательно-параллельное) соединение операций, что рядом со
сложными маршрутами обработки увеличивает длительность производственного цикла. Однако
непотокове производство имеет свою сферу применения, оно широко
используется в промышленных дискретных процессах. За небольших объемов
изготовление отдельных изделий, непоточный метод обеспечивает лучшее использование
оборудования, более полное его загрузки во времени и по мощности, поскольку
обработку предметов можно распределять между станками группы с учетом их
параметров. Поточное производство - высокоэффективный метод организации
производственного процесса. По условиям потока производственный процесс осуществляется в
максимальном соответствии с принципами его рациональной организации. Потоковое
производство имеет следующие признаки:
а) за группой рабочих мест
закрепляется обработка или сборка предметов одного наименования или
ограниченного количества наименований конструктивно и технологически подобных
предметов;
б) рабочие места размещаются
последовательно по ходу технологического процесса;
в) технологический процесс имеет высокую
поопераційну дифференциацию, на каждом рабочем месте выполняется одна или
несколько похожих операций;
г) предметы труда передаются с операции на
операцию поштучно или небольшими транспортными партиями в соответствии с ритмом работы,
что обеспечивает высокую степень параллельности и непрерывности процесса. Широко
применяется специальный межоперационный транспорт (конвейеры), который выполняет не
только функции перемещения предметов, но и задает ритм работы.
Поточные методы применяются для
изготовление продукции в значительных объемах и в течение длительного времени, то есть в
массовом и крупносерийном производстве.
Основным структурным звеном
поточного производства является поточная линия - технологически и
организационно-выделена группа рабочих мест, которая производит один или несколько
подобных типоразмеров изделий. Поточные линии бывают разными, поэтому их
классифицируют по определенным признакам.
По номенклатуре изделий поточные
линии разделяют на одно - и многопредметные. Однопредметною называется линия, на которой
обрабатывается или состоит изделие одного типоразмера в течение длительного времени.
Для перехода на изготовление изделия другого типоразмера необходима перестройка
линии (перестановка оборудования, его замена и т.д.). Применяются эти линии в
массовом производстве. Багатопредметною является поточная линия, на которой одновременно или
последовательно изготовляется несколько типоразмеров изделий, сходных по конструкции и
технологией производства. Сфера применения - серийное производство.
По степени непрерывности процесса
поточные линии подразделяются на непрерывные и прерывные. Непрерывным является линия,
на которой предметы труда перемещаются по операциям непрерывно, то есть без между
операционного ожидания (параллельное сочетание операций). Перериваною, или
прямоточной, считается линия, что не может обеспечить непрерывной обработки
предметов через асинхронность операций. Между операциями с различной производительностью
предметы труда ждут своей очереди на обработку, образуя периодически оборотные
запасы.
По способу поддержания ритма
различают линии с регламентированным и свободным ритмом. На линии с
регламентированным ритмом предметы труда передаются с операции на операцию через
точно фиксированное время, то есть по заданным ритмом, который поддерживается с помощью
специальных средств (преимущественно конвейера). Регламентированный ритм применяется
на непрерывных линиях. На линиях со свободным ритмом предметы с операции на
операцию могут передаваться с отклонением от расчетного ритма. Общий
ритм в этом случае обеспечивается стабильной производительностью рабочего на
первой операции линии или ритмичной сигнализацией (звуковой, световой).
В зависимости от места выполнения операций
линии делятся на линии с рабочим конвейером и конвейером со снятием предметов
для их обработки. Рабочий конвейер, кроме транспортировки и поддержания
ритма является непосредственным местом выполнения операций. Это прежде всего сборочные
конвейеры. Конвейеры со снятием предметов характерны для процессов, операции которых
выполняются на технологическом оборудовании.
По способу перемещения выделяют
конвейеры с непрерывным и пульсирующим движением. Конвейер с непрерывным движением имеет
постоянную скорость и во время работы не останавливается. Конвейер с пульсирующим движением
во время выполнения операций стоит неподвижно. Он приводится в действие периодически
через промежуток времени, равный такту линии. Такие конвейеры применяются
тогда, когда по технологическим условиям выполнения операции требует недвижимого
состояния предмета труда.
Перемещать сами предметы не всегда
возможно и целесообразно (например, за сборки крупногабаритных машин). В этом
случае организуется стационарный поток, когда изделия устанавливаются неподвижно на
сборочных стендах, а перемещаются специализированные группы (бригады) рабочих,
которые выполняют определенные операции. Количество групп (бригад) рабочих равна
количества стендов.
Внедрение поточного производства
требует определенных условий. Основные из них такие:
- достаточный по объему и
продолжительностью выпуск продукции;
- высокая стабильность и
технологичность конструкции изделия;
- возможность рационального
размещение рабочих мест и четкая организация их обслуживания;
- применение прогрессивной
технологии, механизация и автоматизация процессов.
На основании анализа продукции, ее
объема, состояния технологического процесса, возможностей его совершенствования, массы и
габаритов изделия выбирается определенная разновидность поточной линии и исчисляются
основные параметры: такт, ритм, количество рабочих мест, длина рабочих зон,
скорость движения конвейера.
Вычисляя время работы непрерывных
поточных линий, надо предусматривать периодические кратковременные перерывы в работе
конвейера для отдыха рабочих.
Если предметы труда передаются не
поштучно, а транспортными партиями (n),
то они сходят с линии за интервал времени, что называется ритмом линии.
В случае когда организуется
непрерывная поточная линия, после расчета такта проводят синхронизацию
операций. Операции считают синхронизированными, когда продолжительность каждой из них
равно или кратной такту линии. Синхронизация операций достигается
употреблением ряда технологических и организационных мероприятий: дифференциацией,
концентрацией операций, сокращением их продолжительности за счет определенных
усовершенствований и т.д.
Скорость конвейера, который движется
непрерывно, ограничивается рациональным режимом труда. На пульсирующем конвейере,
который включается периодически, она устанавливается с учетом максимальной
правил безопасности труда.
На рабочем конвейере с непрерывным
движением при выполнении операции рабочий передвигается за ходом конвейера в пределах отведенной
ему рабочей зоны. После окончания операции рабочий возвращается к началу
зоны и выполняет операцию над следующим изделием, которое на этот момент должно подойти
до нее. Длина рабочей зоны вычисляется по формуле
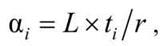
где
αi - длина рабочей зоны на i-й
операции, м.
За обработки или сборки небольших
изделий и малой скорости движения конвейера рабочий может находиться (сидеть) на
одном месте. Например, сборка часов, монтаж радиоаппаратуры и др.
Пространственное размещение поточных
линий может быть различным в зависимости от количества рабочих мест, типа транспортных
средств, площади участка (цеха). Самым простым и распространенным является прямолинейное
размещение рабочих мест по ходу технологического процесса. Но это не всегда
возможно, поэтому бывает двухрядное, кольцевое, зигзагообразное их размещения. Смежные
поточные линии нужно размещать так, чтобы было удобно транспортировать предметы
труда между ними. По организации потоковой обработки и сборки изделий
вспомогательные линии, обеспечивающие сборочный конвейер, размещают перпендикулярно
к нему.